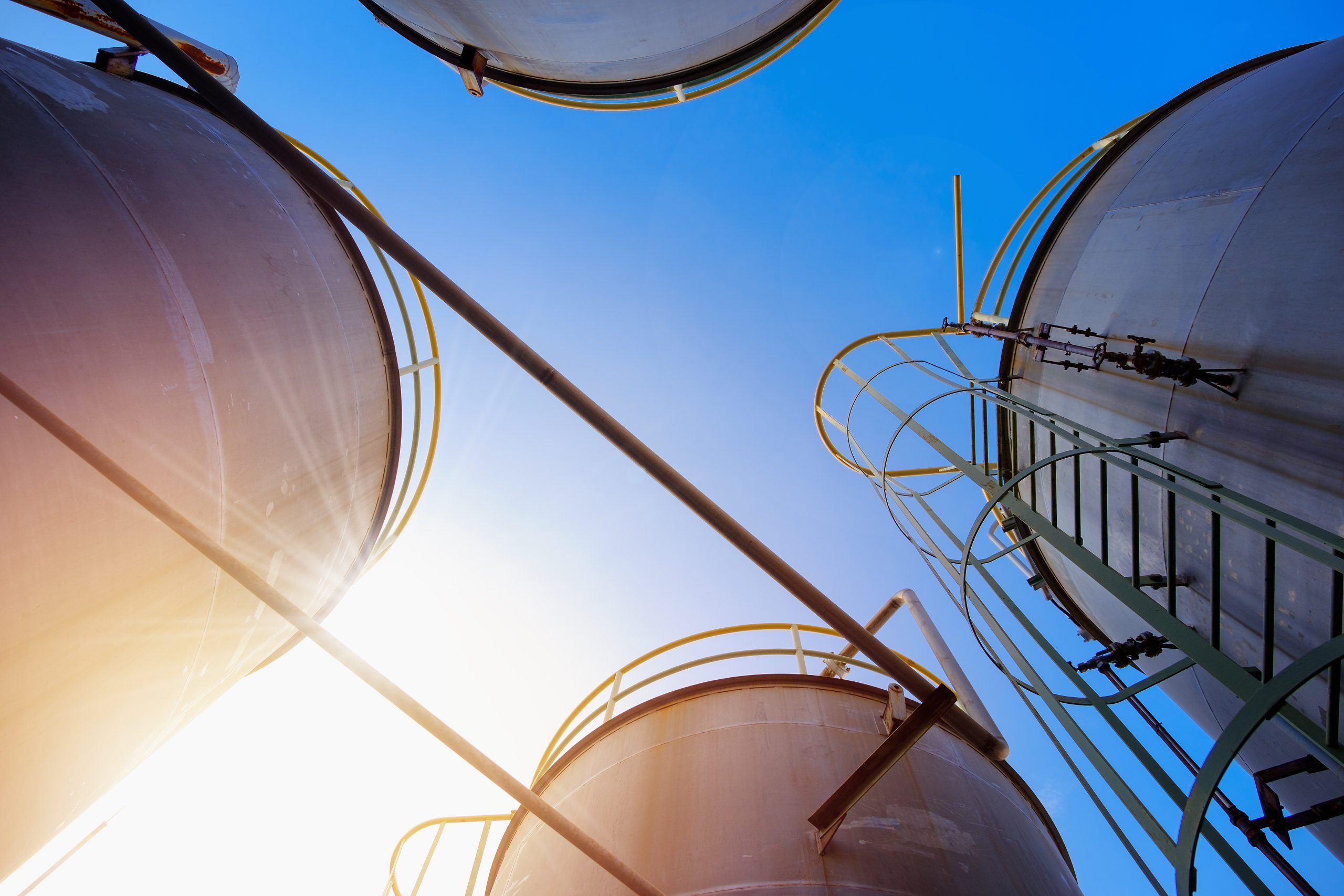
What’s That – Automatic Tank Gauge (ATG)
Do you know what’s in your bulk storage tank? Are safety and efficiency top priorities for your business? If you have bulk fuel storage at your locations, then you may already be familiar with today’s topic – the automatic tank gauge (ATG). An automatic tank gauge (ATG) is a highly effective operational device for monitoring conditions inside your fuel tank. When you need to know details on everything going on inside your fuel tank, from inventory levels to temperatures to tank integrity, you’re going to need to check the ATG.
What is an ATG, and how does it work?
An automatic tank gauge (ATG) is a device used to monitor and measure the level of liquid in a storage tank. It is typically used for petroleum and chemical storage tanks in industrial settings. The ATG can track various aspects such as fuel level, volume and temperature, water level, and volume and issue alerts for high or low fuel levels. Advanced features can be incorporated into the ATG, such as monitoring the interstitial spaces in tanks and piping, overseeing pressurized piping, or enabling remote communication capabilities. Common ATGs on the market include Veeder-Root, Pneumercator, ProGauge, Evo, and more.
The ATG system consists of several components, including a probe inserted into the tank, a console displaying the tank level information, and a communication system allowing the console to transmit the data to a remote location. The probe measures the liquid level and temperature in the tank and sends the data to the console. The console then calculates the volume of liquid in the tank and displays the information in real time. Some ATG systems also include alarms and automatic shutdown features to prevent overfilling or other safety hazards. Overall, an automatic tank gauge helps ensure accurate and efficient inventory management of liquid storage tanks and provides safety measures for storing and handling flammable or hazardous liquids.
Some devices on tanks only report inventory and temperature, without covering compliance issues such as interstitial monitoring and sensor alarms. While some would consider these devices ATGs, others would draw a distinction between a full-service ATG device and a simple tank probe for inventory monitoring.
Do All Tanks Need ATGs?
Not every tank has an ATG. For underground storage tanks (USTs), ATGs are a regulatory requirement. The EPA mandates that UST operators track inventory levels, interstitial space, and other factors to monitor for leaks. Because the tank is underground, a visual inspection isn’t enough – you need sensors to prevent an environmental incident such as fuel leaking into the ground or groundwater.
For aboveground tanks, typically an inventory monitor (also called a tank probe, and sometimes also called an ATG) is sufficient for your needs. Because a leak would be visibly apparent, the government is less stringent about tracking and reporting. Still, some customers may choose to install an ATG for preventative maintenance and for environmental peace of mind.
Main Functions of an ATG
1. Compliance Tracking and Monitoring
Compliance tracking and monitoring is crucial for storage tanks to ensure they are meeting regulatory requirements. An ATG can help with accurate compliance testing, leak detection, and pump flow rate monitoring, all of which are necessary for inspections. Additionally, the ATG can deliver data required by inspectors and even print physical copies of the data at set intervals.
2. Inventory Management
Inventory management is another significant advantage of an ATG. It provides real-time and accurate inventory management, which is essential to prevent losses due to contamination, leaks, or theft. Unlike a tank probe, which is typically battery operated and connects to the cloud at pre-set intervals, an ATG is wired into the tank’s power and can be “polled” at any time to collect an inventory reading.
Gasoline, diesel, and other petroleum products undergo significant expansion and contraction due to temperature changes. To obtain precise measurements, an ATG system must closely monitor the temperature of the fuel. However, the temperature of the delivered fuel typically differs from that of the fuel in the storage tank. As a result, the fuel temperature inside the tank experiences rapid changes after delivery. An accurate ATG reading can only be obtained after the fuel temperature has stabilized, which typically takes 6 to 12 hours after the delivery.
For instance, a temperature change of 1°F can cause 10,000 gallons of gasoline to change in volume by 7 gallons. The actual volume of fuel at any given temperature is known as the gross volume, while the net volume refers to the amount of fuel that would be present in the tank if the fuel temperature were 60°F. For inventory control purposes, the gross volume is the appropriate measurement to use.
This article is part of Daily Market News & Insights
Tagged:
MARKET CONDITION REPORT - DISCLAIMER
The information contained herein is derived from sources believed to be reliable; however, this information is not guaranteed as to its accuracy or completeness. Furthermore, no responsibility is assumed for use of this material and no express or implied warranties or guarantees are made. This material and any view or comment expressed herein are provided for informational purposes only and should not be construed in any way as an inducement or recommendation to buy or sell products, commodity futures or options contracts.