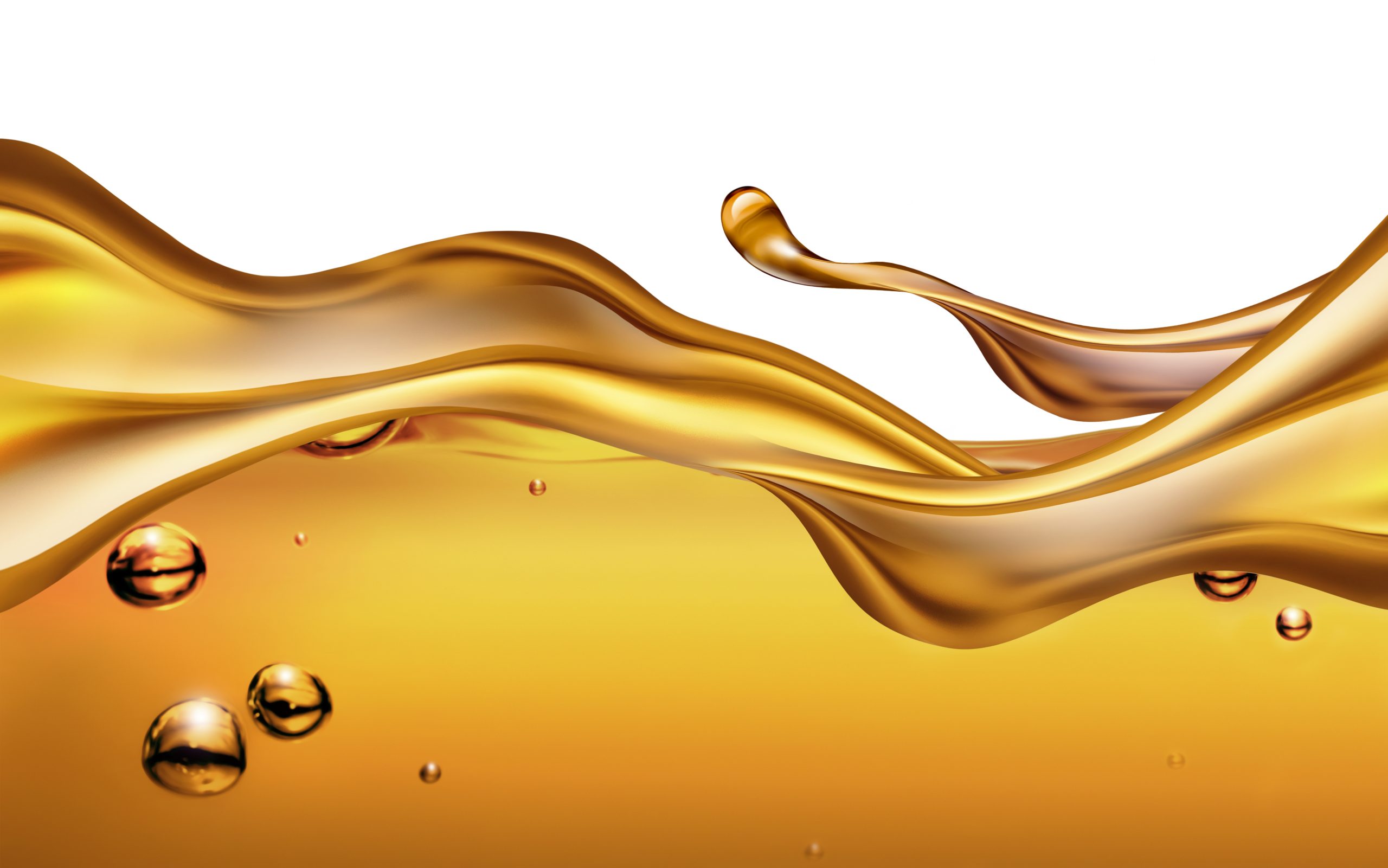
What is it – Fuel Retains
Your fuel driver pulls onto the lot, parks by your fuel tank, and sticks the tank to check the current inventory. They unload the hoses needed to make their normal FTL delivery, and connect the hoses to your tank. The fuel begins flowing out of the truck, and the driver watches attentively to make sure all goes well. But unfortunately, out of the 7,500 gallons of diesel fuel on the truck, only 5,000 makes it into your tank.
Why was only part of the load delivered, and what happens to the remaining fuel? In today’s edition of FUELSNews What Is It Wednesday, we will be covering the concept of fuel retains, how they might be incurred, and how we can prevent them from happening.
What is a Fuel Retain?
A fuel retain occurs when a full truckload of fuel is not delivered completely. Imagine ordering 7,500 gallons of fuel for a storage tank but only receiving 5,000 gallons. The remaining 2,500 gallons stay on the truck – stranded without a home.
It’s important to realize that full truckload fuel deliveries are generally all-or-nothing. Unlike tankwagons, most FTL trucks do not have a gauge that indicates how much fuel has been dispensed. They know 7,500 gallons went in at the terminal according to the BOL, and they know they’re empty at the end. If something happens to stop the delivery midway through, the only way to accurately assess the amount dropped is by comparing before-and-after inventory readings in the tank, which can be an inexact science.
Common Fuel Retain Scenarios
One of the most common causes of fuel retains is under-sized fuel tanks. As you may know, a 10,000-gallon tank only has 8,000 gallons of usable storage space due to overfill prevention. That leaves a very tight window for re-ordering. You re-order when your inventory reads 4,000 gallons, expecting to keep drawing down the tank before the delivery arrives. But for some reason – holiday, weather issues, etc – you don’t use enough fuel. The truck shows up with 7,500 gallons, but you can only fit 5,000 in your tank.
Another possible cause is an inaccurate tank gauge. If your tank has shifted, or your probe is giving inaccurate readings, you might think you can fit a whole delivery when you can’t. In this case, the driver may catch the misreading manually by sticking the tank, or she might use the tank gauge reading and begin delivering. This situation can be more problematic, potentially resulting in a spill if the drop is not stopped off immediately.
Sometimes, a fuel retain can happen for reasons outside your control. A premature closure of the fuel compartment, interruption of the system air pressure during unlading, or parking on uneven surfaces and hinder the fuel delivery. These challenges can be harder to catch, so it’s important to confirm from inventory data that the full delivery was made.
Logistical Challenges Caused by Retains
Fuel retains create logistical challenges for carriers. When retains occur, the carrier can’t simply take the fuel back to a terminal to return it. Carriers often have to make decisions on the fly about how to manage that retained fuel. One common approach is to divert it to other customers who might be in need of that specific amount of fuel. While this might sound like an efficient solution, in practice, it’s not always straightforward. Matching the exact quantity and type of retained fuel with a customer’s immediate need can be challenging, especially if the retain is a relatively small amount or of a less common fuel type.
In situations where a direct match isn’t available, the retained fuel might end up sitting on a truck. This waiting period isn’t merely a static pause; it causes a ripple effect in the carrier’s operations. Carriers need to find a backup solution, which can be a time-consuming process. Every hour that a truck is idled with retained fuel is an hour lost in delivery schedules, leading to potential delays for other customers down the line.
These unnecessary wait times aren’t just an operational hassle for carriers; they also translate to increased costs. Fuel carriers operate on tight schedules and thin margins. Delays mean wasted fuel, increased labor costs, and potential late delivery penalties. Customer satisfaction can be adversely impacted if retains become a frequent occurrence.
The Cost of Retains
Depending on who is at fault during a retain, they can be costly for customers. When sites order fuel they can’t fit, they’re creating a burden on the carrier – one that might be charged to them in additional fees. For instance, a carrier may require the customer to pay for the freight bill on all 7,500 gallons, even if they don’t charge for the actual fuel left on the truck. If it takes hours or days to find an alternative tank, a demurrage fee could be assessed. For that reason, customers should be careful to avoid fuel retains whenever possible. Of course, if the carrier’s equipment was at fault, the cost would not be passed on to the customer.
Avoiding the Fuel Retain Pitfall
Ensuring the accuracy of fuel delivery is a shared responsibility between the fuel delivery company and the fuel-site operator. The most important way to prevent a retain is by checking the inventory before ordering and making sure it will fit. If your tank is too small for your needs, consider expanding it so you have a safety period of a few days between being able to fit a full load and running out of fuel.
When your truck driver arrives, they should check your inventory again to confirm the load will fit. This action prevents a spill, and may also make the process smoother if a retain is inevitable. They can keep one compartment closed, giving them a more accurate picture of exactly how much fuel they will be retaining. While this won’t alleviate the logistical concern, it can make the billing process smoother.
Ultimately, the objective is to have fuel deliveries that are both safe and precise. By following proper ordering procedures, making sure tanks are the right size to fit a full load, and maintaining safe and effective equipment, fuel buyers can progressively eradicate fuel retain issues. This not only ensures safer and more efficient deliveries but also reassures all stakeholders that they are genuinely receiving what they’ve paid for.
Fuel inventory management is essential for unlocking your business’s true potential. If you don’t have digital insights into your fuel tank, Mansfield can help install the right equipment to give you the visibility you need to avoid a retain.
Mansfield’s fuel management platform, FuelNet, offers operational and financial visibility to improve fuel management. It helps you easily track bulk fuel and DEF purchases, as well as repair and maintenance, all in one place. FuelNet empowers you to take control of your fuel management, simplifying processes and increasing efficiency for your business.
Don’t waste another minute on inefficient fuel management. Contact us today and discover how we can fuel your success.
This article is part of Daily Market News & Insights
Tagged:
MARKET CONDITION REPORT - DISCLAIMER
The information contained herein is derived from sources believed to be reliable; however, this information is not guaranteed as to its accuracy or completeness. Furthermore, no responsibility is assumed for use of this material and no express or implied warranties or guarantees are made. This material and any view or comment expressed herein are provided for informational purposes only and should not be construed in any way as an inducement or recommendation to buy or sell products, commodity futures or options contracts.